The programmable controller of the stepper motor is directly controlled, which can significantly reduce the cost of the automatic production line control system of the combined machine tool.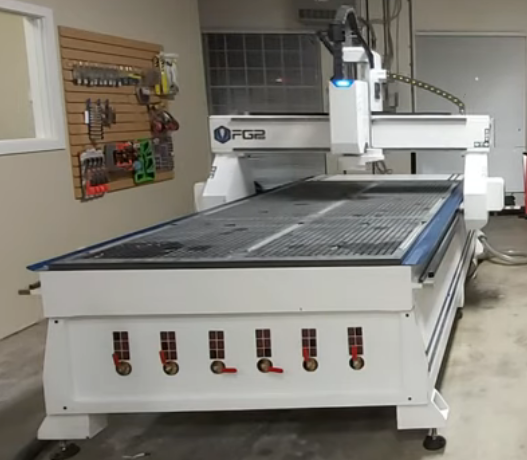
Below we introduce the numerical control slide table method of using PLC to control the stepper motor drive, servo control, drive and interface, and the software logic of stepper motor PLC control.
1. Overview
In the automatic line of the combined machine tool, three sliding tables are generally set according to different machining accuracy requirements
(1) Hydraulic slide table, used in rough machining processes with large cutting volume and low processing accuracy requirements;
(2) Mechanical slide table, used in semi-finishing processes with medium cutting volume and certain processing accuracy requirements;
(3) CNC slide table, used in the finishing process with small cutting amount and high processing accuracy requirements.
Programmable controller (PLC) is widely used in industrial automatic control due to its strong versatility, high reliability, simple command system, easy to learn programming, easy to master, small size, less maintenance work, convenient field interface installation and a series of advantages. Especially in the control of the automatic production line of the combination machine tool and the S, T, M function control of the CNC machine tool, it shows its excellent performance.
PLC-controlled stepper motor open-loop servo mechanism is applied to the CNC slide table control on the automatic production line of the combined machine tool, which can eliminate the numerical control system of the unit and reduce the control system cost of the unit by 70~90%, and even only occupy 3~5 I/O interfaces and <1KB memory of the automatic line control unit PLC. Especially in large automatic lines, the cost of the control system can be significantly reduced.
2. What are the structural components of PLC-controlled CNC slide table?
PLC-controlled CNC slide table structure
Generally, the CNC slide table in the automatic line of the combined machine tool adopts an open-loop servo mechanism driven by a stepper motor. The numerical control slide table with PLC control is composed of programmable controller, circular pulse distributor, stepper motor driver, stepper motor and servo transmission mechanism.
PLC is used to realize the direct control of stepper motor
The gears Z1 and Z2 in the servo transmission mechanism should take anti-backlash measures to avoid reverse dead zone or reduce the processing accuracy; The lead screw drive pair should determine whether to choose the ball screw pair according to the processing accuracy requirements of the unit. The ball screw pair is adopted, which has the advantages of high transmission efficiency, good system rigidity, high transmission accuracy and long service life, but the cost is high and it cannot be self-locking.
3. What are the PLC control methods of CNC slide table?
PLC control method of numerical control slide table
There are three main control factors for CNC slide tables:
3.1. Stroke control
Generally, the stroke control of hydraulic slide table and mechanical slide table is realized by using position or pressure sensors (stroke switch/dead block iron); The stroke of the CNC slide table is realized by digital control. It can be seen from the structure of the CNC slide table that the stroke of the slide table is proportional to the total angle of the stepper motor, so as long as the total angle of the stepper motor is controlled. From the working principle and characteristics of the stepper motor, it can be seen that the total rotation angle of the stepper motor is proportional to the number of control pulses entered; Therefore, the number of pulses output by the PLC can be determined according to the displacement of the servo mechanism:
n= DL/d (1)
where DL - the displacement of the servo mechanism (mm), d - the pulse equivalent of the servo mechanism (mm/pulse)
3.2 Feed speed control
The feed speed of the servo mechanism depends on the speed of the stepper motor, and the speed of the stepper motor depends on the pulse frequency of the input; Therefore, the pulse frequency output by its PLC can be determined according to the feed speed required by the process:
f=Vf/60d (Hz) (2)
Vf - feed speed of the servo mechanism (mm/min)
3.3 Feed direction control
Feed direction control is the steering control of the stepper motor.
The steering of the stepper motor can change its steering by changing the energization sequence of each winding of the stepper motor; For example, the three-phase stepper motor is energized in A-AB-B-BC-C-CA-A... Stepper motor forward rotation; When the winding presses A-AC-C-CB-B-BA-A... The stepper motor is reversed when the sequence is energized.
Therefore, the output sequence of the hardware loop distributor can be changed by the directional control signal output by the PLC, or the power-on sequence of the stepper motor winding can be changed by programming to change the order of the output pulse.
4. Software control logic of PLC
It can be seen from the PLC control method of the slide table that the total number of input pulses and pulse frequency of the stepper motor should be controlled accordingly.
Therefore, a pulse signal generator with controllable total number of pulses and pulse frequency is set on the control software; For control pulses with lower frequencies, timers in the PLC can be used to construct them, as shown in Figure 2. The pulse frequency can be controlled by the timing constant of the timer, and the total number of pulses can be controlled by setting a pulse counter C10.
When the number of pulses reaches the set value, the counter C10 action cuts off the pulse generator loop and stops working. The stepper motor of the servo mechanism stops running when there is no pulse input, and the servo actuator is positioned. When the displacement speed of the servo actuator is required, the high-speed pulse generator in the PLC can be used. Different PLCs, the frequency of high-speed pulse can reach 4000~6000Hz. For the general servo mechanism on the automatic line, its speed can be fully satisfied.
PLC is used to realize the direct control of stepper motor
5. Servo control, drive and interface
5.1. Composition of stepper motor control system
The control system of the stepper motor consists of a programmable controller, a circular pulse distributor and a stepper motor power driver.
PLC in the control system is used to generate control pulses; Output a certain number of square wave pulses through PLC programming, control the rotation angle of the stepper motor and then control the feed of the servo mechanism; At the same time, the pulse frequency is controlled by programming - the feed speed of the servo mechanism; The circular pulse distributor distributes the control pulses output by the programmable controller to the corresponding windings in the power-on order of the stepper motor.
PLC-controlled stepper motors can either use a software circulating distributor or a hardware circulating distributor as shown in Figure 1.
The use of soft rings occupies a lot of PLC resources, especially when the phases of the stepper motor windings M>4, should be fully considered for large-scale production lines.
Using hardware loop distributor, although the hardware structure is slightly more complicated, but can save the number of I/O port points occupying PLC, there are a variety of special chips available in the market.
The stepper motor power driver amplifies the control pulse output by the PLC to tens ~ hundreds of volts, several amps ~ ten amperes of driving capacity.
Generally, the output interface of PLC has a certain driving capacity, while the load capacity of the usual transistor DC output interface is only tens ~ tens of volts, tens ~ hundreds of milliamps.
However, for the power stepper motor, the drive capacity of tens ~ hundreds of volts, several amps ~ tens of amps is required, so the driver should be used to amplify the output pulse.
5.2. Interface of programmable controller
If the servo mechanism adopts a hardware circulating distributor, the number of I/O port points occupying the PLC is less than 5 points, generally only 3 points. Among them, the I port occupies a little point as a start control signal; The O port occupies 2 points, one point is used as the pulse output interface of the PLC, connected to the clock pulse input end of the hard loop of the servo system, and the other point is used as the steering control signal of the stepper motor and connected to the phase sequence distribution control end of the hard loop, as shown in Figure 3; When the servo system adopts a software circulating distributor.
6. Application examples and conclusions
The PLC-controlled open-loop servo mechanism is used for the CNC slide table of a large production line, each slide table only occupies 4 I/O interfaces, saving the CNC control system, its pulse equivalent is 0.01~0.05mm, and the feed speed is Vf=3~15m/min, which fully meets the process requirements and processing accuracy requirements.